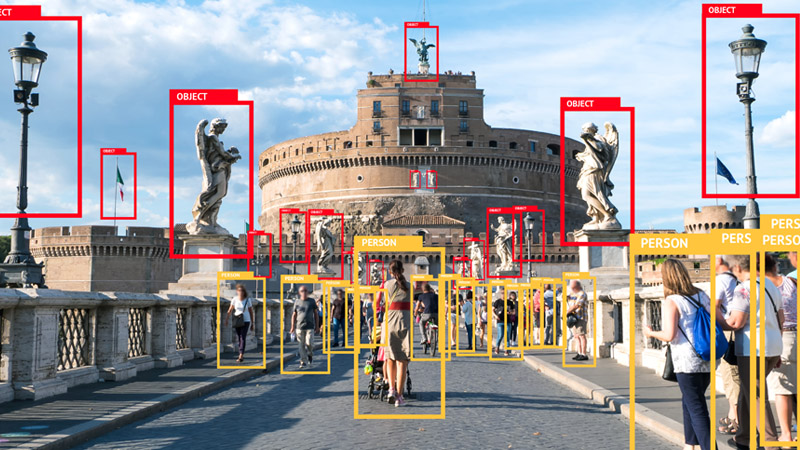
New Website
Created a new personal website to share ideas and projects!
Passively supporting prosthetic devices for locomotion have been around for centuries. Two decades ago, the first microprocessor-controlled knee prosthesis (MPK) introduced a new generation of passive assistance. Some studies showed that the users of MPKs producing variable damping, i.e., variable breaking torques, experience biomechanical improvements during their locomotion, such as an enhanced smoothness of gait and a decrease in hip work production. Despite the suggested benefits, the research has been inconclusive about the general advantages of MPKs regarding non-microprocessor-controlled knees (NMPKs). For both NMPKs and MPKs, there are still common deficiencies when comparing the passive gait of prosthetic users with the gait of healthy subjects. Both users perform compensatory movements during day-to-day activities that result in asymmetric loading between both limbs. On the long term, this can lead to secondary complications such as back pain. One reason for these compensatory movements, is the lack of active assistance during their locomotion. This establishes the opportunity to move from passive prosthetic devices to more capable active designs that also produce driving torques.
Active behaviour of the knee prosthesis could impel equal loading, which in turn means a reduction of these compensatory movements. It is also suggested that an active knee could furthermore result in a lower energy consumption of the users during activities such as stair ascent. Although there is much potential, general claims on the benefits of active knees still require more research. One reason for this is that the benefits strongly depend on the appropriate use and integration of actuators, sensory systems, and the control scheme. Therefore, it is interesting to explore new design concepts and develop different active control strategies.
The Direct Coupling Design (DCD) includes a newly developed electric drive which consists of a Permanent Magnet Synchronous Machines (PMSM) connected to a three stage planetary gearbox. This drive will control the driving torque, speed and position of the knee to acquire the active behaviour of the knee joint.
The goal of this work is to design and simulate an active force control architecture for an electric drive.
Created a new personal website to share ideas and projects!
Co-developing new multi-objective expensive optimization algorithm
Meetups for AI researchers within the LUMC
Multi-objective deformable image registration in oncology